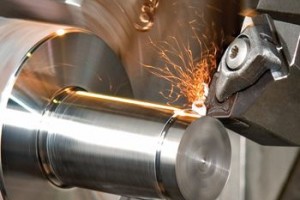
CNC Insert Wear Some Tips for CNC Operators
CNC machines are used for continuous and accurate job production. So to keep this a continuous process some sophisticated tooling is used like tools with the Inserts. The machining with inserts is easy, because the CNC machine operator just has to change the insert and not the entire tool (as tool change on the CNC machine is not an easy process) so the setting time is now much less than a complete tool change.
Inserts also has a life, after a time (this time depends on the material of the workpiece and the coolent quality) inserts began to wear, meaning it began to change its shape a bit.
It is obvious if the insert will change its shape or insert wears the accuracy of the job will also suffer. So insert is usually checked by the cnc operator after couple of components,
if the insert wear is small then the cnc machine operator will make some change in the tool offset of the specified tool (the wear offset change process is cnc machine dependent) this will ensure that the job will be of the same size as are specified in the component drawing.
But if the insert wears too much now the surface finish of the job will suffer but the job dimensions might be accurate, but this will also not be acceptable to have jobs accurate in dimension but not in surface quality. So now the insert change is reasonable.